How robotic process automation increases competitiveness
Despite the acknowledged productivity benefits of automation, many companies still handle common business practices manually, missing out on efficiencies and potential competitive advantage. Organisations should consider robotic process automation for back-office operations, and even some front-office processes, which are currently still done manually, according to NICE.
Gerry Tucker, managing director, ANZ, NICE, said, “Businesses can gain significant benefits by automating certain business processes through robotic process automation. There are two types of robots: attended robots, which are used on a desktop to help humans optimise their work; and unattended robots, which live on the server and replace human activity. Using attended or unattended robots can help organisations deliver a consistent customer experience and makes workers more efficient.
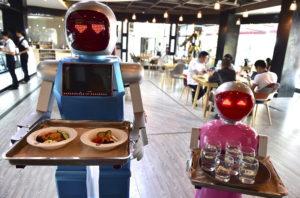
“For example, one of the world’s largest furniture retailers worked with NICE to implement a robotic process automation solution that could streamline order entry and fulfilment for customers. The system eliminated 100 per cent of order entry errors. It automated the processes and tasks associated with the equivalent of 16 full-time employees, letting those workers focus on more value-adding tasks.
In total, the robots reduced the company’s manual workload by 5,000 hours per year, delivering a faster, more accurate automated order and delivery system. This dramatically improved the customer experience.”
Robotic process automation has been defined by the Institute for Robotic Process Automation as “the application of technology that allows employees in a company to configure computer software or a ‘robot’ to capture and interpret existing applications for processing a transaction, manipulating data, triggering responses and communicating with other digital systems”.1
NICE has identified five ways robotics can improve an organisation’s business processes, enhance the customer experience and deliver greater employee satisfaction:
- Increasing employee satisfaction: By relieving employees of repetitive, menial actions, organisations can improve customer service and employee satisfaction at the same time. Employees can focus on different and more interesting work, rather than doing admin or routine jobs.
- Reducing time and improving customer experience: By eliminating lengthy manual tasks and replacing them with faster, automated processes, employees can complete more work in less time, providing higher-quality customer service faster. This increases customer satisfaction and saves money, ensuring the company can remain competitive.
- Reduce errors: Human error is virtually unavoidable in manual processes. Automation through robotics not only eliminates errors but ensures that the process is completed in the same way every time. In turn, this means less time and money is wasted, leading to greater customer satisfaction.
- Increase revenue: By letting customer-facing employees have the right conversations with customers at the right time, businesses can increase revenue. For example, when a customer calls to update their address and add an authorised person to their account, robotic processing automation presents the agent with additional information about the caller. This gives them the information they need to recommend a relevant product or service to the customer at the right time.
- Enable compliance: Robotic processing automation mitigates the risk of data compromise that goes hand-in-hand with manual manipulation of customer information. With automation, the risk of non-compliance, data loss, or data compromise is greatly reduced. This saves time and money, and ensures the company’s reputation remains intact.
Gerry Tucker said, “Robotic processing automation lets robots perform basic, rules-based tasks so humans can focus on more value-added tasks. The robots can operate 24/7 without breaks, making them far more cost effective than human operators and even more cost effective than offshore providers. Furthermore, robotic processing automation provide strong governance and auditability because it enables detailed and real-time traceability of all process steps.”