Building the case for manufacturing automation to drive business growth
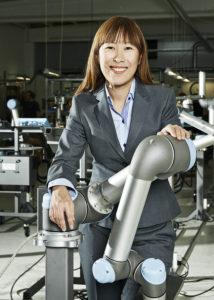
By Shermine Gotfredsen, General Manager SEA & Oceania, Universal Robots
New Zealand’s manufacturing industry has continued to expand almost every month since October 2012, based on the Bank of New Zealand-Business NZ performance of manufacturing index . The sector was lifted by a construction boom that started during the rebuild of Christchurch post-earthquake.
However, manufacturing as a percentage of the economy has declined in the long-term, from about 26 percent of gross domestic production (GDP) 40 years ago to about 13 percent in 2009 . To ensure manufacturing momentum continues, New Zealand manufacturers must look to innovative new ways to achieve business growth and expansion into regional and international markets.
Recent research from Universal Robots, which surveyed the Australian and New Zealand manufacturing community indicates a growing emphasis on automation and particularly robotics as a way to increase competitive advantage.
Almost half of ANZ manufacturers have invested in automation in the past year. Meanwhile, a vast majority of manufacturers plan to invest in automation in the coming year, with more than half of those respondents planning to install robotics solutions.
This growth in automation investment has no doubt been driven by an increased focus on business innovation. Due to New Zealand’s geographical isolation creating higher freight overheads, and greater labour costs compared to countries such as China, many local manufacturers have felt pressure to consider automation as a way to increase productivity and profits.
The decision to automate is typically based on a number of factors, namely the need to improve business performance, reduce production time and improve the quantity and quality of output.
One such company exploring the use of automation to enable greater production flexibility and output is Auckland based injection moulding company TCI New Zealand, which deployed Universal Robots cobots to help automate specific production processes, such as labelling and installing rubber feet on its containers and yoghurt makers.
Using UR cobots several key processes in the manufacture of these products have been automated, relieving employees of repetitive assembly processes and ensuring smooth production flow. The cobots can be completely reprogrammed and deployed for new tasks in a matter of minutes.
Cobots in particular can provide greater ease of use and are able to work closely alongside human workers unlike traditional robotic solutions. This means shop floor applications can be quickly adapted to suit changing workflow needs.
Today’s leading manufacturers are highly agile in order to adapt to changing market demands. With the use of cobots, companies are able to adapt to the demands and whims of the market.
That is, they are able to decrease or increase product cycle times to suit consumer demand.
Unlike legacy industrial automation working behind cages, cobots can be quickly and easily assigned to new work stations and tasks based on changing production needs, helping to reduce costs related to downtime.
Before choosing an automation solution, it’s also important to consider product quality and assurance, particularly if planning to involve robots with tasks involving product assembly.
Cobots for instance, offer high levels of quality control, which is particularly important for food manufacturers. The new lightweight industrial robots has a repeatability of plus-minus 0.1mm, which significantly reduces the time employees need to spend on manual quality checks and prevents the wastage of food or packaging, for example.
Automation and in particular cobots offer not only the potential to improve operational efficiency, but also greater agility and flexibility to adapt to meet changing markets demands and achieve business growth.
While geographical isolation and talent shortages continue create barriers to business expansion, there’s a no better time than now for New Zealand manufacturers to consider automation.