Workplace distancing solution to manage “next normal” manufacturing
Manufacturers are facing new challenges as they restart or maintain operations due to the Covid-19 pandemic.
As preparations are made for the “next normal”, manufacturers must consider additional dimensions of employee safety, including the establishment of production environments and workflows that address physical distancing requirements.
Combining proven hardware and software, Siemens has created a new solution that enables companies to quickly and efficiently model how employees interact with each other, the production line and plant design.
The new solution also enables organisations to build an end-to-end digital twin, to simulate worker safety, iterate on and optimise workspace layouts and validate safety and efficiency measures to help future-proof production lines.
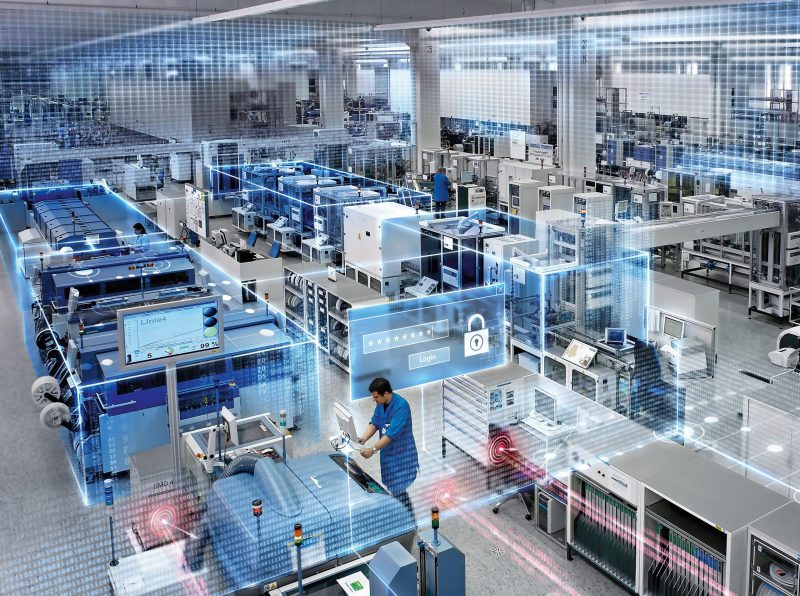
With Siemens’ SIMATIC Real Time Locating Systems (RTLS), companies can continuously measure distances between workers, provide real time visual feedback to employees regarding their spacing from others and create a log of all movements and interactions over time.
In this way the Siemens’ SIMATIC RTLS continuously facilitates safe distancing while providing numerous additional benefits.
Combining SIMATIC RTLS with a digital twin of the actual manufacturing environment permits companies to model and simulate how employees interact with the equipment and each other, enabling them to iterate and optimise safety and productivity in the short term, and validate a redesign of the entire operation before more costly physical changes are made.
In order to implement this solution, Siemens’ SIMATIC RTLS transponders are embedded in badges which are worn as personal protective equipment by all employees. RTLS receivers placed throughout the operation can then continuously track and record workforce movement.
When two employees are in a risk scenario (e.g., less than six feet apart), their badges will display a warning, alerting them to the situation. The data collected over time can be analysed to identify “hot spots” where risk scenarios occur frequently.
Such situations become easily actionable via the digital twin, which is provided by Siemens’ Tecnomatix Process Simulate and Plant Simulation software. Utilising the collected data, new manufacturing layouts or workflows can be simulated until one is determined to provide the desired outcomes, which can then be implemented in the physical operation.
Beyond this, manufacturers can add traceability to the solution through Siemens’ on-premise solutions or an application such as Siemens’ Trusted Traceability Application on MindSphere, the cloud-based, open IoT operating system which helps enable rapid, comprehensive contact analysis in the unfortunate event of an actual workplace illness.
All movement and contact with the affected employee can be visualised, enabling rapid notification of those who came into close contact and selective (rather than site-wide) deep cleaning of exposed physical environments.