Reimagining supply chains to build long term resilience in a post-Covid world
By Richard Morgan, Country Manager, Genpact
The Covid-19 pandemic has disrupted all facets of supply chains. Whether it is in the retail, telco, or transport industries both global and local supply chains have been severely tested, having to adapt to new demand patterns, supply constraints and logistical challenges.
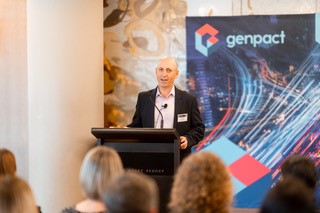
This unprecedented disruption has only magnified changes in consumer behaviour, under-investment in supply chain tools, technology, and people that were already challenging organisations.
As the risk landscape is set to only get more uncertain and complex in the future, building resilient and more agile supply chains is crucial.
Learning the Covid-19 lessons
If Covid-19 has taught us something is that the strength of a supply chain is only as good as its weakest link.
Organisations must use the current disruption as an opportunity to do a full audit and assess how well its supply chain functions can better respond to future disruptions.
To build long term resilience companies must re-examine their old supply chain assumptions and evaluate the strength of their end-to-end supply chains. Businesses need to fine tune demand planning, search for deeper visibility of material planning, test supply planning technologies and continuously evaluate logistics plans.
Supply chains must move from executors and a cost centre to a source of competitive advantage that unlocks operational margins and builds stability in an uncertain world.
Stabilising supply chains: a cross collaboration with risk management teams
To address the volatile nature of current – and likely future – supply chain operations, organisations should start by mobilising a dedicated crisis and risk management team that can help advise supply chain teams.
A cross collaboration with risk management experts can help build focused risk scenarios and assessments, as well as design new processes and frameworks for rapid replanning, demand forecasts, supplied engagement and reporting and governance.
Working side by side with risk management teams will also help supply chain teams prioritise issues for resolution.
Using technology and data-driven decisions to build long term resilience
In today’s connected world, making informed decisions is highly dependent on being able to analyse and make sense of data points collected throughout the supply chain.
Implementation of digital and data-driven technologies such as artificial intelligence (AI) is what will allow businesses to reimagine and future-proof their supply chains in an unstable world.
The differing impact of Covid-19 across states, countries, and regions has created more hyper-local and time-sensitive demand patterns, making demand-sensing abilities more critical than ever.
Therefore, all dimensions of demand-sensing data must improve – in terms of accuracy, timeliness, completeness, reliability, and relevance Demand-forecasting models must be fine-tuned to ingest these unique patterns and rapidly revise demand forecasts.
In addition, current conditions have highlighted the need for better visibility of the availability and capacity of suppliers and contract manufacturers across multiple tiers. Organisations should combine control-tower solutions, capacity data, and delivery-performance data to analyse and assess their cumulative risk across supplier tiers for parts, ingredients, and finished products.
Understanding these risks will help organisations create a vertically integrated risk profile of finished products that enables proactive corrective actions such as finding alternate suppliers, minimizing SKU proliferation, and simplifying input material design and production.
Finally, as demand forecasting and deeper material planning continue to respond to new patterns, organisations should sweat their existing technology landscape to provide more robust analysis for allocating and distributing finished products.
Modelling tools such as Kinaxis, E2open, OM Partners, and o9 can provide extensive allocation-scenario analysis, and flag fulfilment risks so help take corrective actions for production plants and suppliers.
Over the past few years, the guiding principle of cost efficiency has had a major impact on supply chain design. Higher-risk tolerances have been sacrificed to reduce costs.
The pandemic has highlighted this approach’s fragility, leaving no other options but to look at other models to build long-term resilience. A closer collaboration with risk teams, as well as a better end-to-end management of data across complex supply chains is what will reduce cost and risk, ultimately building that resilience while maximising revenues.