Filtration face off: Melt-blown fibres versus electrospun nanofibres
New research into the effectiveness of melt-blown fibres and electrospun nanofibres has found nanofibre filter media provides significantly increased protection against bacteria and viruses such as Covid-19.
The research, conducted by Dr Fabrice Karabulut from Revolution Fibres in New Zealand, contrasts and compares nanofibre filtration with traditional melt blown filters in light of increased global demand for PPE and the future need for more effective face masks.
Dr Karabulut says melt blowing, a commercially successful and low-cost process for producing filtration microfibres, produces fibres with diameters in the range of 1-10 micrometres.
“The structure of a melt-blown filter is like a non-uniform fishing net. Its pores are 1-3 micrometres in diameter which are much larger than bacteria and viruses which are just 0.1 micrometres.”
He says the diameters of nanofibre range from 10 – 300 nanometres, which is 10 – 100 times smaller than conventional melt-blown microfibres, meaning they are very effective in protecting against viruses such as COVID, bacteria and other toxic particles.
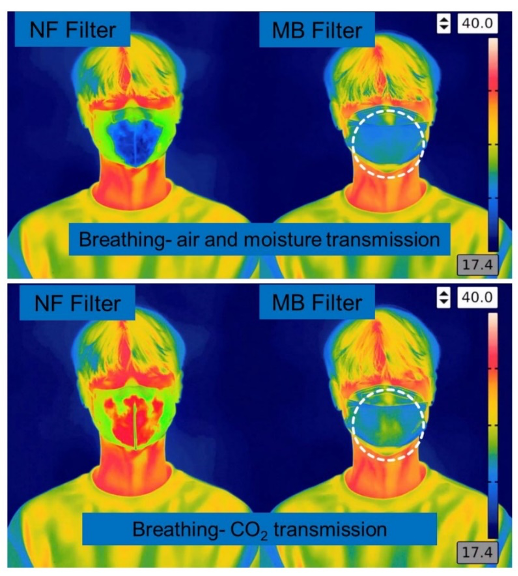
“Electrospun nanofibre is characterised by a very large surface area and small pore diameter which significantly increases the probability of particles in the smaller, submicron and nanometre range depositing on the fibre surface – thereby improving filter efficiency.”
Increased breathability and reusable
Dr Karabulut’s research is contained in the White Paper Melt-Blown Fibres vs. Electrospun Nanofibres as Filtration Media which outlines the differences between nanofibre filtration capability and melt-blown filtration.
As well as increased filtration performance, he also found the breathability and reusable nature of nanofibre made it superior to melt-blown filtration. “The current pandemic has amplified the need for masks to be reusable but retain effectiveness,” he says.
“A recent study testing the reusability of melt-blown and nanofibre filters when cleaned with ethanol showed melt-blown filters were only effective for single use due to the steep reduction of filtration efficiency after ethanol cleaning. This is because the electrostatic charge of these types of filters is lost when cleaned, leading to a dramatic drop in performance.
“On the other hand, it was found electrospun nanofibre filters can be successfully reused multiple times after cleaning with ethanol as the filtration efficiency remains consistent.”
Wide ranging functionality
Nanofibres are highly controllable with the electrospinning process enabling management of qualities such as absorbency, fibre diameter and surface area. Modification of these parameters allow them to filter higher amounts and a wider range of particles and contaminants than melt-blown filters.
In addition, electrospun nanofibres have low basis weight, high permeability, and tight pore size that make them appropriate for a wide range of filtration applications. This broad use extends to other applications ranging from skincare and medical uses to strengthening and acoustic sound absorption.
Meeting global demand
When the impact of Covid-19 escalated in March, Revolution Fibres pivoted its business to accommodate large scale filter media production for N95 face masks to help bolster PPE supply both in New Zealand’s local market and overseas.
Filtration for respiratory protection from pollution and viruses is what Revolution Fibres made its name on 10 years ago, leading the commercialisation of nanofibre technology in New Zealand with product lines such as air filtration for home ventilation company HRV.
Revolution Fibres advanced SETA filter media is able to trap 99% of microscopic particles such as spores, allergens, and bacteria.
Revolution Fibres CEO Ray Connor says adapting its filter media for face masks required specialist development as well as increasing production capacity to meet the high levels of local and international demand.
With the proliferation of counterfeit face masks globally, Connor says Revolution Fibres is also making a concerted effort to ensure its product is fully compliant with the most stringent standards including NIOSH, EN, and ASTM (N95 to N99).
“Filtration plays an important role in purifying and decontaminating two life necessities: water and air. As awareness of the related health issues has increased, and accelerated by the current COVID-19 pandemic, the demand for protection from air-borne pollution and disease has also increased.”
Commercially viable
Mr Connor says historically nanofibres were not able to be produced in large enough volumes and at low enough cost to be commercially viable up against existing alternatives such as melt-blown.
“Recently technology advancements have meant production rates of electrospun nanofibre are close to that of the conventional melt-blowing process.
“Internationally, the nanofibre market is continuing to grow which is why we have scaled up to increase production to meet demand for not only filter media but our full suite of products.”