Industry 4.0 Adaption to NZ Industry
Dr Mike Edmondson, Founder, Edge Robotics and Automation Ltd
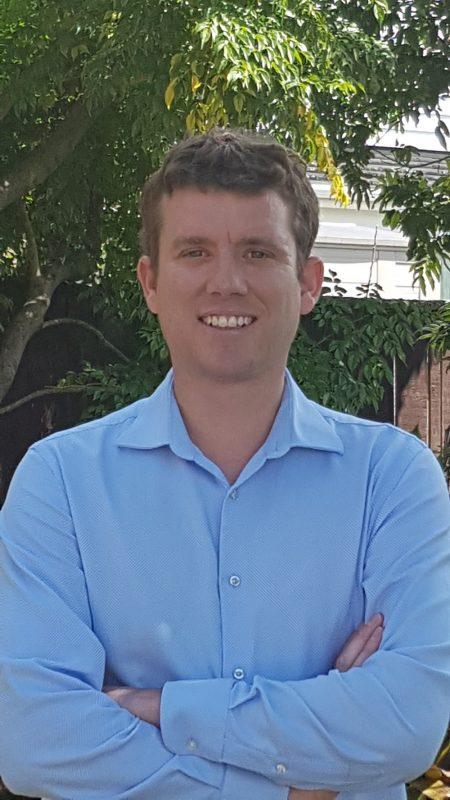
One thing I commonly find is the lack of widespread direction and grasping of “Industry 4.0” benefits in the context of NZ industry. The rapidly changing world is hard enough for technical experts, let alone for manufacturers to filter and identify how to use this potential.
The drive for improvement from manufacturers and wider industries is certainly present and has been growing with the push from COVID.
Here are three topics for our industry, with the hype removed and practical opportunities we could apply:
Robotic Automation
It is particularly surprising how big a disconnect there is between your typical production manager or GM and the actual costs and capability of robotic systems.
Enquirers are often surprised at the modern cost of purchasing industrial robots let alone the opportunities offered with current state-of the-art.
The total economics become even more prevalent when an integrator has the innovation skills to take a robot centric approach.
This allows you to capture all the additional indirect benefits such as flexibility and reducing both the capital and operating costs.
NZ has a great history of successful innovation and leading the world, however, part of the very fabric of that innovation mindset tends to hurt in scaling. Often, we do not value our time or get side-tracked away from our core business trying to reinvent the wheel.
Industrial Robots are an easy way to scale and are highly advanced, flexible mass-produced units that come off a production line with 60 odd years of refinement.
Leading brands have reliability statistics of 7+years between failure and depending upon the chosen manufacture local factory support.
Then you factor in the indirect benefits such as being able to repurpose and reduce complexity of an overall system. The flexibility of robotics allows the reduction of moving parts in an overall system.
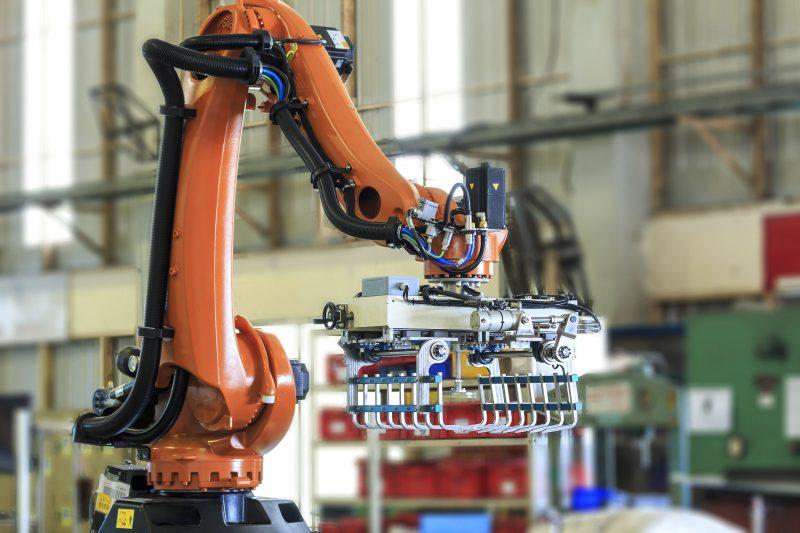
This significantly saves engineering hours, expensive custom one-off builds often with rework, and greatly increasing system reliability by reducing those untested custom parts.
A good example is a system that had two similar functioning 2D scanning systems. A robot actuated system and the other fixed automation integrating your typical PLC/Servo and an off the shelf gantry.
Initially the robot approach looked expensive having this big visible cost. By the time both were complete the robot system had a total cost 40% less, was more accurate, faster and flexible.
Then, like clockwork, a change was required; a few minutes on the robots and all done, vs redesign parts, rework and ordering new parts.
Not all applications will be so extreme, but in this case the robot system almost did not make it past initial brainstorming due to not carefully considering the total time to production.
Another common theme of Industry 4.0 is the mass customisation via the interconnection of systems; this can be considered differently to help NZ manufacturers make use of industrial robotics in our smaller scale operations.
The growing prevalence of database connections to automation equipment allows the opportunities for dynamic reconfiguration of systems on the fly; in essence reprogram the robot per batch.
A skilled integrator will be able to create program templates that can then be automatically adjusted and mix ’n’ matched from production ordering systems.
Whereas a cobot may need full manual “reprogramming” per small job; the more intelligent robot can handle a wider range of operations without any human intervention at all.
Some of our disconnect for the cost and capability of robotics is certainly historic, and the other growing element is the effect of cobot hype.
The cobot narrative pushed has compared their benefits against what industrial robotics where over 20 years ago and this is spilling over to reinforce historic connotations.
Years ago, when I completed my industry-based PhD program, industrial robots were frustratingly limited, nowadays, if I can dream it, the robot can probably do it.
Numerous misconceptions are prevalent; the big point to correct is requiring robots to be caged has not be true for a very long time, and another example is robots can often be factory equipped with hand guidance.
Readers could search for Kuka’s Safe operation or ABB’s Safemove2 to get an idea on state-of-the-art. Human interaction with robots is not a black and white caged, or collaborate application as narratives suggest, but a range that spans from fixed guarding, coexistence, cooperation, and finally true collaboration.
The overwhelming majority of “collaborative applications” come under the coexistence or cooperation technical definitions.
Skillset consideration aside, there is an entire article worth cutting through the hype in terms of operation and programming.
In the case of coexistence and cooperation, modern industrial robots will generally be the better solution in term of performance, reliability, cost, and a good bet they will have double the lifespan of a cobot.
Depending upon the situation, industrial robots, or if your budget extends to cobot prices, hybrids such as FANUC’s CR series can still complete true collaboration tasks and maintain robot advantages.
Likewise, full cobots are not intrinsically safe as per hype suggests, and you still need to know what you are doing.
Attending numerous tradeshows even several automation companies have had unguarded cobots moving around with incorrect safety and demonstrating common mistakes of not considering the full workspace or risks posed by grippers and their impact area (i.e., head height).
None of this means cobots are a bad solution, they are a big technical leap and a great enabler to new application.
We have several cobot systems out for proposal on suitable applications. The important factor is not buying into hype or marketing campaigns but to objectively look at your application.
A skilled robotics integrator will be able to develop an understanding of your operations and help come up with the optimal solution. There can also be a very wide range of costs involved; for larger 1M+ projects then your Tier 1 & 2 automation providers are your only reasonable option.
Lesser scale, thou not necessarily simpler projects, can often be handled by smaller integrators providing much better value and more hands-on support.
Edge Robotics and Automation is also happy to help those undertaking projects predominately inhouse providing opportunities for significant cost reduction.
Machine Learning
Machine learning is one technology that often goes hand in hand with this wider discussion of Industry 4.0. Many “in-production” machine learning applications are more around the financial and operational space of companies such as production modelling and preventative maintenance.
This pattern will increase into the future, but realistically, still quite a few steps away from transformational changes to a big portion of our industry.
NZ and Australia have another opportunity since our industries are heavily towards the primary and secondary industries, and often even our later manufacturing has natural components.
Key to applying automation in these industries is the capability of systems to move away from fixed numerical decision-making, and towards those that work with subjective or chaotic environments.
In essence, the automation system needs a “feel” of a process or to reason as per an operator; and this is what machine learning can offer.
Despite the recent hype, machine learning has been lurking in these industries for over a decade, it just has not been publicised and players have kept it under wraps for competitive reasons.
Media often builds up the picture of some magical invention with Will Smith fighting a glowing white ball.
In reality, machine-learning is “just” a field of mathematics based around the self-tuning of equations. Each application is typically a customised pattern with different base equations and tuning methods.
The pattern technically referred to as a model, will be based around KPIs such as accuracy, stability, disturbance rejection, plus the practicalities on the amount of data collection and tuning (cka training) time.
Various means of producing machine learning models exist from simple software wizards to full expert level development. Most in-production industrial machine learning systems work on cloud or server setups, however, recent products like new TwinCat features from Beckhoff allow expert level models to operate on standard automation controllers.
As a nation we have the technical capability to gradually roll out the advantages, ideally from lowest hanging fruit and up.
The difficulty is connecting the computer science trade with the wider range of industry groups and there are simply not many people who can cross that boundary.
Vision systems
Automation companies should these days have minimal trouble doing a basic integration of smart cameras and this works great in a carefully controlled manufacturing environment.
Get closure to natural products and the mass market vision systems fall over. Machine learning has been a great aid to vision systems by allowing more subjective measurements.
3D systems are another vast range of technologies that get attention, and if you know the tricks, these can also simplify and reduce the overall cost of more conventional problems.
As with many leading technologies it is important to looking beyond the marketing and get a better understanding of the limitations and challenges that are not immediately obvious.
Beyond this we barely scratch the surface of what is possible with machine vision due to our own limited perception of the world.
The road to truly mastering vision applications occurs once you go beyond the notion of human sight. In many cases difficult problems, or those that we think are random, become clear when we know where and how to look.
Non-Visible UV or Infra-Red is not just one grey type but has variations like colour and this has many uses with sorting and quality control in natural products.
Using UV light for example can lead to fluorescence of contaminants and bacteria, all normally invisible to our eyes and colour cameras.
Using polarisation properties like your sunglasses, provides the chance to look at internal structural defects in transparent materials, packaging seal quality or microscopic surface details.
Measuring these principles are no longer the domain of solely scientific equipment but available in off the shelf industrial components at reasonable prices.
Some of these principles can be applied to standard equipment for a few hundred dollars, yet you would be none the wiser unless you know where to look.