Manufacturing in the age of sustainability
For companies to be truly sustainable, they not only need to limit the impact of the manufacturing process but create products that benefit society, writes Iain Hosie.
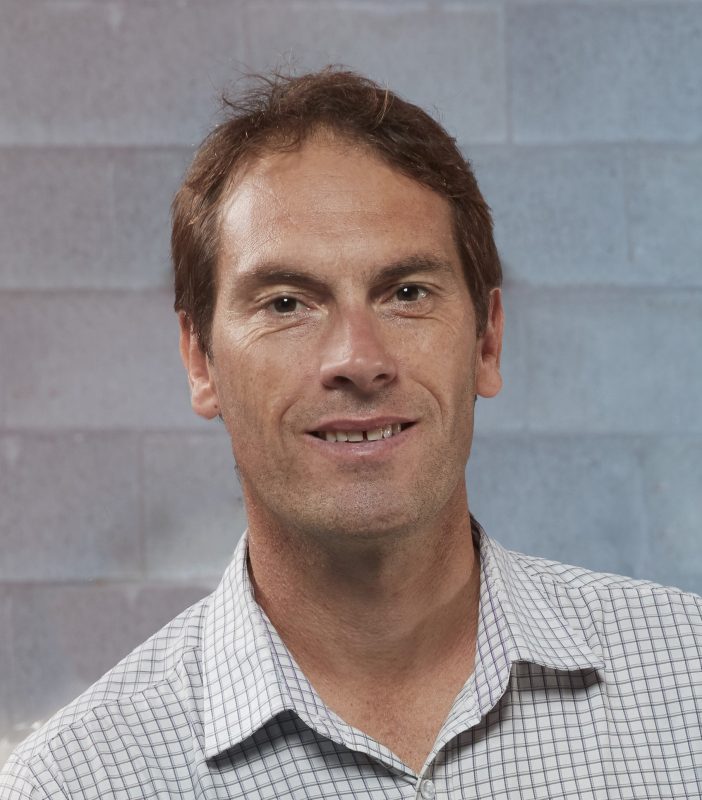
Globally, the heat is on companies to continue to reduce waste and prioritise sustainability when developing or manufacturing products.
Constantly fine-tuning processes and researching new, environmentally friendly methods is essential to making this change happen.
So, using safer, less toxic solvents, or monitoring and changing production processes to reduce the amount of waste going to landfill, is great. But as a manufacturer, there is more to sustainability than being clean, green, and doing your bit for climate change.
Key to being a sustainable business is creating a range of products and applications that make a difference in society – while also working to limit its impact on the planet.
Companies and manufacturers also have an opportunity to influence and encourage sustainable customer behaviour through the way they design and produce their products. This needs to be an increasingly important consideration for manufacturers if they want to be taken seriously in the sustainability stakes.
Take the unique technology behind Revolution Fibres’ nanofibre skincare product, ActivLayr, which uses collagen to deliver natural actives deep into the skin. This is in stark contrast to the excessive amount of chemicals found in traditional creams and serums.
ActivLayr technology also has strong potential beyond the skincare industry. With the ability for different ingredients to be added to the ActivLayr formula it could one day enable a controlled drug dose to be delivered to a patient for more effective and efficient treatment.
The beauty of nanofibre – a class of textile made from superfine fibres 1/500th the width of a human hair which can create vast changes in strength, reactivity, and absorbency – is that it can be used to enhance a wide variety of products. From skincare and the highest quality filtration media that exceeds N95 standards, through to strengthening Formula One car.
In the textiles sector, nanofibre offers distinct advantages because the volume used to create materials is a fraction of what is needed using traditional textiles. One kilogram of polymer can create a nanofibre that would reach to the sun!
As a manufacturer, using sustainably sourced and bio-derived materials is an ideal starting point. For example, ActivLayr uses sustainably sourced premium New Zealand marine collagen.
In face masks, the unexpected fashion trend of 2020, nanofibre filtration provides better protection than traditional melt blown filters. They can also be used for up to 200 hours compared to the 72 hours recommended for common N95 masks, which significantly reduces the number of masks going to landfill at a compatible price.
Nanofibre also helps make products stronger – and last longer. Composite strengthening nanofibre improves the durability and lifetime of products and is used in everything from space rockets to cars and fishing rods.
There is no finish line when it comes to sustainability. However, constantly innovating and striving to create products and applications that truly benefit society can help to ensure a strong sustainable legacy.