Is NZ’s Covid response world class?
By Ian Walsh, Managing Director, Intent Group Limited
The re-emergence of Covid-19 in our community has got me thinking, as I am sure it has many of you. Of course, our normal reaction is to leap to solutions to ‘solve’ or eliminate the problem we’re facing, including measures such as shutting the borders, denying travel and so on.
Upon reflection, I’m certain we are thinking the wrong way about how we manage returning New Zealanders.
Is it our objective to fill the available managed isolation capacity to maximise the number of people per capita returning? If so, we’re probably succeeding. Great! We’re truly world class.
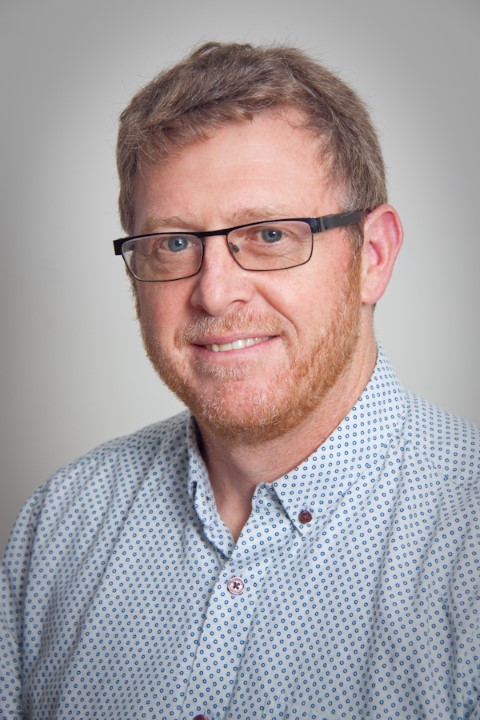
But, if our objective is to ensure that everyone who leaves managed isolation is COVID free, then we’re not so successful.
There is a significant difference between a world class mindset and the ‘also-rans’. A world class company identifies its core objective and aligns all systems and processes to achieve this objective. Inputs, variables and outputs are measured and anything impacting the goal is eliminated. All leading indicators of failure are addressed.
A great example which springs to mind is Alcoa. Paul O’Neil changed the focus of the organisation from output, to safety, with a goal of zero incidents. He was relentless in leading this approach and transforming the organisation, and achieved outstanding safety improvements and exceptional business outcomes, as a result. This leadership lesson is inspirational. I had the privilege of visiting Alcoa’s centre of excellence in Davenport, Iowa, a few years ago, and their culture of safety clearly underpinned everything. It still does.
We can think of managed isolation as a processing facility very similar to a manufacturing or processing plant. The goal is not to maximise capacity, but to deliver quality (by being COVID free). If you were producing food, let’s say baby food, everything you would do first and foremost would be aligned with food safety and quality.
You would ensure the site, plant and equipment was fit for purpose, clean and hygienic; all people and operators would follow the correct cleaning, sanitation and equipment protocols; all ingredients would be tested and certified to ensure they met required specifications; and the manufacturing process would follow agreed QC and QA procedures to ensure compliance with manufacturing instructions.
All packaging would be tested, and the final product examined before release for consumption. Retention samples would be kept, environmental swabbing carried out to ensure cleaning was effective, audits conducted and so on. The goal would be for no one to become ill from consumption of your product.
World class companies achieve 100% compliance, with no safety incidents, minimal loss and waste, no environmental impacts and extremely high efficiencies (over 90%).
In our managed isolation facilities, we are processing people. We have processed a large number with minimal incidents, but there are reports of rooms not left clean, non-compliance with social distancing upon arrival, PPE failures and so on. These are leading indicators of future failure. To achieve zero failure, we need to move the goal from throughput to quality (i.e no one leaves with COVID).
How can we ensure this? Certainly, no one would go into a room that was not certified and tested as sanitised and safe. To be sure, we could leave rooms empty for a period of time to ensure any lingering trace of the virus had decayed. Of course, this would sacrifice some throughput for the real goal of quality.
We could also audit and mandate the correct PPE with zero tolerance for non-compliance. We could provide additional transportation to create social distancing, require returnees to wear additional PPE, and so on.
In our regular briefings we are assured that we have improved our processes, and I am sure we have, but these improvements appear to be a reaction to failures or near misses, rather than a designed system to achieve zero failures.
We should firstly determine what rate of throughput we can sustain without compromising the primary goal (to be COVID free) and then determine what we need to do to safely raise the bar.
Another way of looking at it is this – you would not release a food product that killed people, ever. You would never take the risk and yet it is still possible for COVID-19 to get into our community and do the same.
If this was a manufacturing plant, and perhaps they could and should be considered as high hazard facilities, they would be shut down until they could demonstrate that the required standards are met, in the same way that shops that don’t meet Ministry of Health standards are closed to protect the public.