Additive Manufacturing: Re-thinking how we use materials in a circular economy
By Dr. Jim Goddin, Technical Director of Circular Economy at thinkstep-anz.
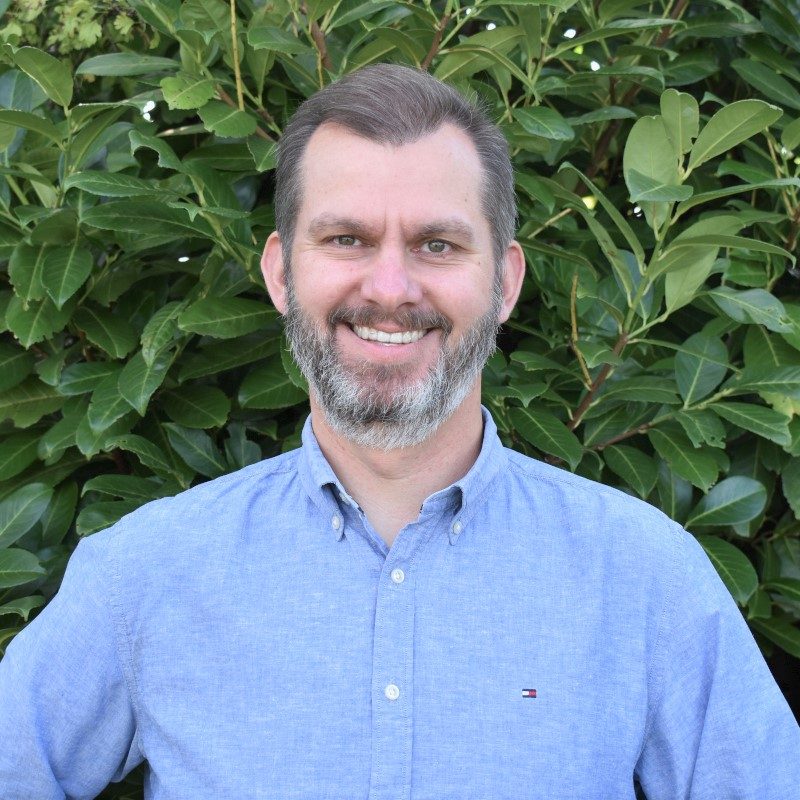
The circular economy presents a more economically sustainable and lower-risk alternative to the highly wasteful, linear, take-make-dispose economy.
The regenerative model proposed by the circular economy shows that when the things we make are designed to last, their economic value can be recovered for the benefit of the business.
If delivered well, the circular economy can also provide significant environmental and social benefits.
The circular economy presents key opportunities for products that rely on advanced manufacturing processes such as Additive Manufacturing. Additive Manufacturing (AM) — sometimes called 3D printing or near-net-shape manufacturing — is the process of building a part layer by layer through selectively fusing (or sintering) the material using a laser or electron beam.
This layer-wise process delivers design freedoms that are unavailable in more traditional manufacturing techniques.
World-leading AM collaborations are incorporating Life Cycle Assessment principles when developing AM processes and parts, including the €18M (NZD $30M) AMAZE project — Europe’s largest and most ambitious metal additive manufacturing research project.
Many AM projects also have a strong focus on resource efficiency. Metrics, such as the Material Circularity Indicator (MCI), enable us to gauge resource efficiency and in turn, quantify how circular products are. How then might AM be promoted based on circularity?
Recovering manufacturing value in a circular economy
The circular economy is estimated to represent a $NZD $7.5T global economic opportunity.
This massive economic value stems from the reduction of supply risks and the recovery of value that is currently lost through products which are designed inefficiently, under-utilised, or which otherwise go to waste.
Recovering materials through recycling is a prominent part of the circular economy and serves an essential purpose in reducing waste.
However, recovering raw material value only accounts for a tiny portion of the circular economy’s economic potential. The more significant value for most products is the value added to the materials through manufacturing.
This is especially the case for products that rely on advanced manufacturing processes such as Additive Manufacturing (AM).
Recycling doesn’t recover the manufacturing value. This is why the circular economy places a greater emphasis on:
- reducing the use of materials in the first place
- reusing or remanufacturing products and parts
- creating durable products that deliver value for longer.
AM can be a key enabler for these so-called ‘inner loops’ of the circular economy.
Reducing material use with AM
As a technique, AM focuses on the minimisation of materials and the optimisation of the product.
In rapid prototyping, AM enables the production of whole assemblies in one go that would have previously required the manufacture of expensive, specialist tooling for each iteration.
This approach is already widely adopted in the automotive sector by the likes of BMW. Air New Zealand also used this technique in collaboration with Auckland based Zenith Tecnica to rapidly prototype metal framing for their Business Premier cabin.
In production, AM can produce highly optimised designs that only contain the amount of material necessary to facilitate the desired function.
This is achieved by using materials simulation and topological optimisation — a mathematical process that optimises the material layout within a volume for a given set of loads.
The ability to deliver optimised, lightweight designs has been a significant selling point for AM in the aerospace and automotive industries where weight reductions can provide substantial fuel savings and additional performance.
Fuel savings are also part of the circular economy, which mandates a shift to renewable energy use and away from the linear burning of fossil fuels.
The initial use of AM often resulted in a significant waste of the material powders used, which tend to oxidise when removed from the machine’s inert environment.
Now most leading AM machines incorporate ‘in machine’ reuse and recover powder without removing it from the inert gas. This development seeks to deliver additional economic savings by recovering high-value feedstock.
Consuming less material and producing less waste are fundamental principles of the circular economy.
The material savings from reusing powders, avoiding tooling, optimising designs, and reducing fuel burn are tremendous circular economy developments.
Supporting the singles approach
From a manufacturing perspective, inefficiencies can result from multi-material and multi-part products.
Having multiple parts means introducing materials that serve no purpose other than holding the components together.
As well as adding more weight and more time for assembly and disassembly, it also introduces additional points for failure.
AM has already enabled significant part count reductions through integrated builds, where one printed part replaces many components.
For example, by incorporating internal cooling channels, as an AM ice cream mould from Tauranga based RAM3D demonstrates, AM can also reduce the need for complex, multi-material cooling systems.
From a circular economy perspective, products containing multiple materials or material grades tend to be recycled less.
An economic balance exists between the cost of disassembling a product into different materials and the value of the recovered material.
If the cost to disassemble products is greater than the recovered materials’ value, there is a greater chance that the materials won’t be separated. Downcycling is then the most likely result — the materials are recovered at a lower quality and economic value due to cross-contamination.
While there is still plenty of discussion over multi-material AM, the reality is that most manufacturers prefer to dedicate a machine to a single material to avoid the assurance risks associated with powder contamination.
This tendency of AM to utilise single grades of material and reduce disassembly requirements enhances the product’s eventual recyclability. It lends itself to higher quality recycled materials, thus contributing to both facets of the circular economy.
Printing the future green
Increasingly, AM is enabling the printing of parts on demand for various applications.
Print on demand means that there’s no longer the need to maintain a significant inventory of components that might never get used.
It also means that stock will never run out, meaning that legacy products can continue in operation for longer, again fulfilling one of the circular economy’s core requirements.
The powder or filament required for AM can be the same for multiple components across multiple products, therefore minimising the overall need for materials within the business. Inventory for AM can be held anywhere for localised printing, as evidenced by installing an AM machine on the International Space Station.
Getting new parts into space is notoriously expensive, but if you have the material and a printer, you can make whatever you need.
Of course, AM isn’t the best solution for every product. The strategy for selecting AM as a manufacturing route should, however, incorporate circularity and environmental performance.
Methods such as the Material Circularity Indicator (MCI) and Life Cycle Assessment (LCA) ensure that manufacturers can design for these benefits of AM and easily communicate them to the customer afterwards.