Waste: The Enemy of World Class
-Ian Walsh, Managing Director, Intent Group Limited
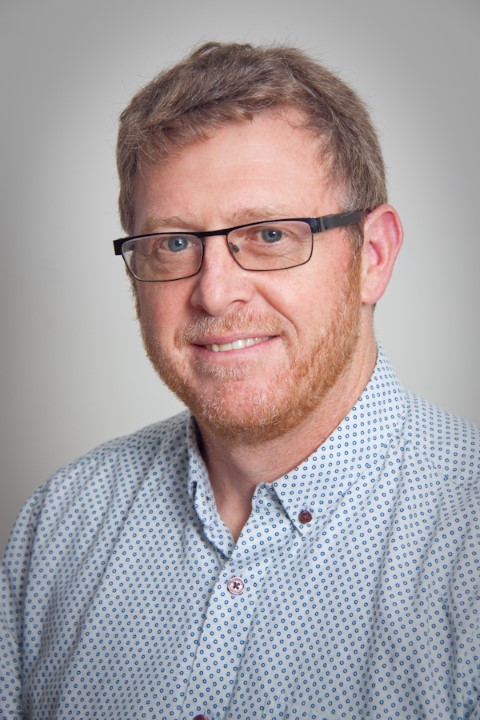
Most practitioners of continuous improvement and “lean” thinking will explain the approach to world class as making value flow by eliminating waste and continuously improving processes, practices and systems to support this value.
Over the last few months, we’ve been made aware of the impending crisis in the horticultural sector – a crushing volume of produce languishing on the vine (or branch) due to a shortage of pickers.
Can you imagine putting all your energy, labour, fertiliser,
sprays, pruning and thinning practices over a whole year and then watching
helplessly as some, or even worse, most of your crop ending up as just
worm food?
What an incredible waste, and yet this is what the industry has faced.
Clearly, this was not the intention of the orchardists; had they known this would be the case, they would have managed their orchards to reduce the costs, efforts and waste.
The problem stemmed from the lack of available labour to pick the crop. When we went into Covid lockdown last year the harvest was nearing or had reached completion.
The emerging problem of lack of labour, due to border restrictions on Recognised Seasonal Employer (RSE) scheme workers, was highlighted and well documented.
Yet in a period of nearly 12 months we were unable to put a process in place to avoid this waste.
The assumption appeared to be that there would be enough labour freed up from other sectors to fill the gap.
With the unemployment rate climbing, mostly through cuts in the tourism and hospitality industries, surely there would be enough people crying out for any employment opportunity they could get?
The reality is this was not the case. Firstly, you’d have to be willing and able to pick fruit. Our nation’s experience over the summer shows this a far less simple requirement than you’d think.
Secondly, you’d have to be willing to relocate to the region that needs you. Thirdly, you’d have to be willing to work when required, and this is weekends and evenings at times.
With these considerations in mind, there simply aren’t that many folks who fit the bill, and certainly not enough to fill the labour gap.
This has been evident to the industry for a long time, who have worked with Work and Income (WINZ) for many years before the problem became insurmountable (unless you are going to apply draconian measures to the labour force such as forced relocation).
The solution was RSE scheme workers, which has been a win-win since 2007. It is not about cost savings, as there are additional costs in utilising this workforce (flights, accommodation etc.)
It is providing labour that the local economy is unable to meet for a period of the year. It provides a good source of income for many of the islands that are in the scheme.
This is much better than letting the fruit go to waste.
This year 14,400 was the number of RSE workers expected (the same as last year, despite huge growth in horticulture).
Of this only 8,000 were available (6,000 who did not go home and 2,000 the government let in).
Given this known labour shortfall, ensuring that sufficient labour was available should have been a huge priority, given the potential revenue, impact on GDP and impact on local economies and people of not realising your crop!
As discussed in previous articles, other countries have a Ministry of Trade which ensures these kinds of crises don’t happen. They ensure that country puts its best trade foot forward, and that the sectors collaborate and co-ordinate to avoid unnecessary waste.
It’s clear now that there was no plan B to mitigate the waste. It’s surprising that many of the (mostly Pacific Island) countries that provide these workers have no Covid issues and we could have had lots of empty isolation hotels in those locations had we chosen to be more proactive.
To exclude these workers and consequently allow this waste is unfathomable and unacceptable.
We have some exceptional produce in NZ. To deliver this quality product to the world we need to eliminate these types of wastes from our value chains and rapidly!
I’m keen: let’s support our growing industries by developing better approaches to deal with these issues in our new Covid world.