Manco Rail boosts NZ engineering sector with multi-million dollar Sydney tunnel contract
Auckland company Manco Rail has given New Zealand’s engineering sector a multi-million dollar boost by securing a contract to supply specialised equipment for two 15 kilometre rail tunnels being built under Sydney Harbour.
Manco Rail won an international tender against Australian and European competitors to supply automated equipment to transport the rail through the two tunnels, lay the sleepers, and then thread the rail onto the sleepers.
All this equipment is radio-remote-controlled. Manco is also supplying the equipment to install the overhead wire to power the trains.
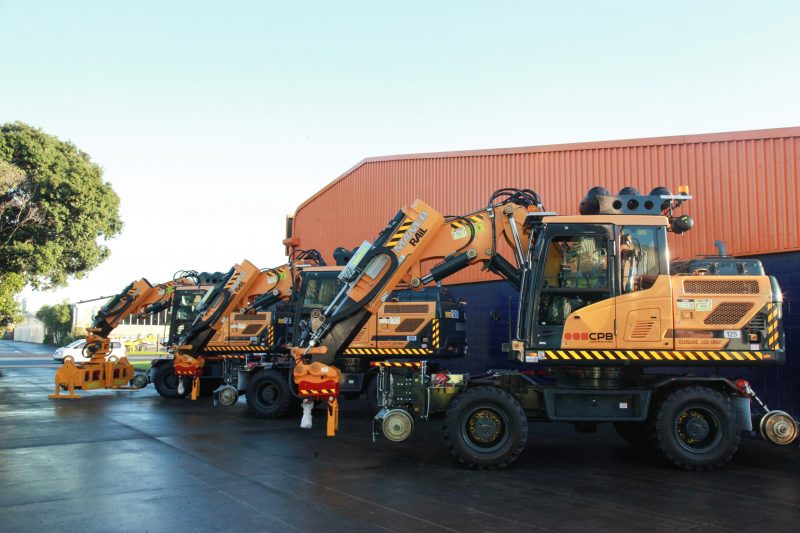
The New South Wales Government, via Sydney Metro Trains, is in the advanced stages of building the north and south tunnels under Sydney Harbour and a significant amount of equipment will be shipped out on 2 July.
Manco Rail managing director Bryan Black said the contract, worth tens of millions of dollars, will secure employment for about 300 people and provide new jobs for the 40 New Zealand companies supplying Manco with components.
“Manco Rail has about 75 employees at three locations in New Zealand but we have three times that number in long-term subcontractor alliances, mainly throughout the North Island. We have taken on six additional university-qualified design engineers, three auto-electricians, and a wide range of skilled engineering personnel from many industries including some redundancies from the airline industry.”
Manco Rail’s subcontractors for the Sydney project include:
- Gaminco, a large Tauranga machining company with world-class facilities which does extensive work for John Deere,
- G90 Engineering and Juno Engineering in Matamata which supply machine and fabricated parts,
- Piako Engineering in Morrinsville which supplies fabricated parts,
- and 35 other New Zealand companies, mostly locally owned, which supply a range of hydraulics, electronics, and radio-control equipment.
Mr Black said the capability of the New Zealand engineering sector is constantly underestimated. “Many of these companies are third-generation and go back to the days when import licensing and strong apprentice programmes created the level of innovation and initiative that prevails today. It is great to see the push for New Zealand manufactured goods at long last following Covid.”
He said the contract was won based on Manco’s decades-long history of supplying proven quality specialised rail equipment, particularly for electrification projects. Manco has designed and supplied rail plant for major projects in Malaysia, Hong Kong, Thailand, and Australia.
“Manco was chosen to design and build semi-automatic specialised plant for numerous construction facets in the Sydney rail tunnels due to the success of Manco-supplied equipment for significant Victorian State rail infrastructure projects in 2017.”
Manco was selected by Systems Connect, a joint venture between CPB Contractors and UGL, that will deliver the laying of track, power, communications, and signalling equipment to the project between Chatswood and Bankstown.
Compounding the standard complexities of installing new track, the project is constrained by having only three major access points for equipment and materials along 31km of tunnels. In addition, gradients in the tunnels are steep, at 4.5 per cent, said Paul Ryan, senior project manager at Systems Connect.
“Construction within this tunnel environment is inherently complex. Access is limited, spaces are confined and grades are steeper. We worked with Manco Rail to custom design equipment that overcomes these challenges,” he said.
Mr Black said winning the Australian contract has helped open new business opportunities for Manco in Australia and New Zealand including a new rail tunnel under the Brisbane River, the Auckland City rail loop and the proposed Papakura to Pukekohe extension.
He said the challenge of increasing rail services in cities where space is at a premium means many are going underground, offering more business opportunities for rail equipment engineering companies like Manco.
For the Sydney tunnels, Manco’s sleeper-laying trailers are equipped with a sleeper-grab straddle, rail threader trailer, tug units, sonar detection systems, and a track guidance system fitted to the equipment.
Developed over 14 months, the custom designed equipment lays the rail, spreads it out, places the sleepers, and then pulls the rail back over the top. The process of developing this one-of-a-kind equipment started with a blank slate.
“The design and interface of each plant item has involved hundreds and hundreds of design hours. Utilising a highly competent team of young mechanical engineers tasked with starting with a ‘clean piece of paper, and fresh ideas’, brainstorming meetings were held on a regular basis, where even the most radical concepts were discussed,” said Black.
“Ultimately, rational thinking prevailed. But the plans still incorporated some of the vast array of technologies available in electronics, motive power, hydraulics, fabrication materials and ergonomics.” The entire process is radio-remote-controlled, crucially limiting the number of people in high-risk areas.
The Manco equipment will be used in two stages. First, it will lay the track components.
Then the track form will be concreted, and mechanical and electrical systems and signalling equipment will be installed. Afterwards, the Manco track-laying equipment will return, including wheel excavators, trailers, and tugs, to assist with concreting activities, and electrical and mechanical installations.